When it comes to high-efficiency workholding in machining, few tools rival the versatility of Kurt’s caged tombstones. Originally developed by Kurt’s Custom Engineered Workholding team to house internal hydraulic lines for automated fixturing, caged tombstones have become a staple in horizontal machining centers.
Offering unmatched benefits for quick-change flexibility and setup efficiency—whether you’re managing a small shop, scaling operations for a mid-sized manufacturing facility, or an OE manufacturer looking for greater throughput—caged tombstones can revolutionize the way you approach complex setups.
Subplates allow quick-change flexibility
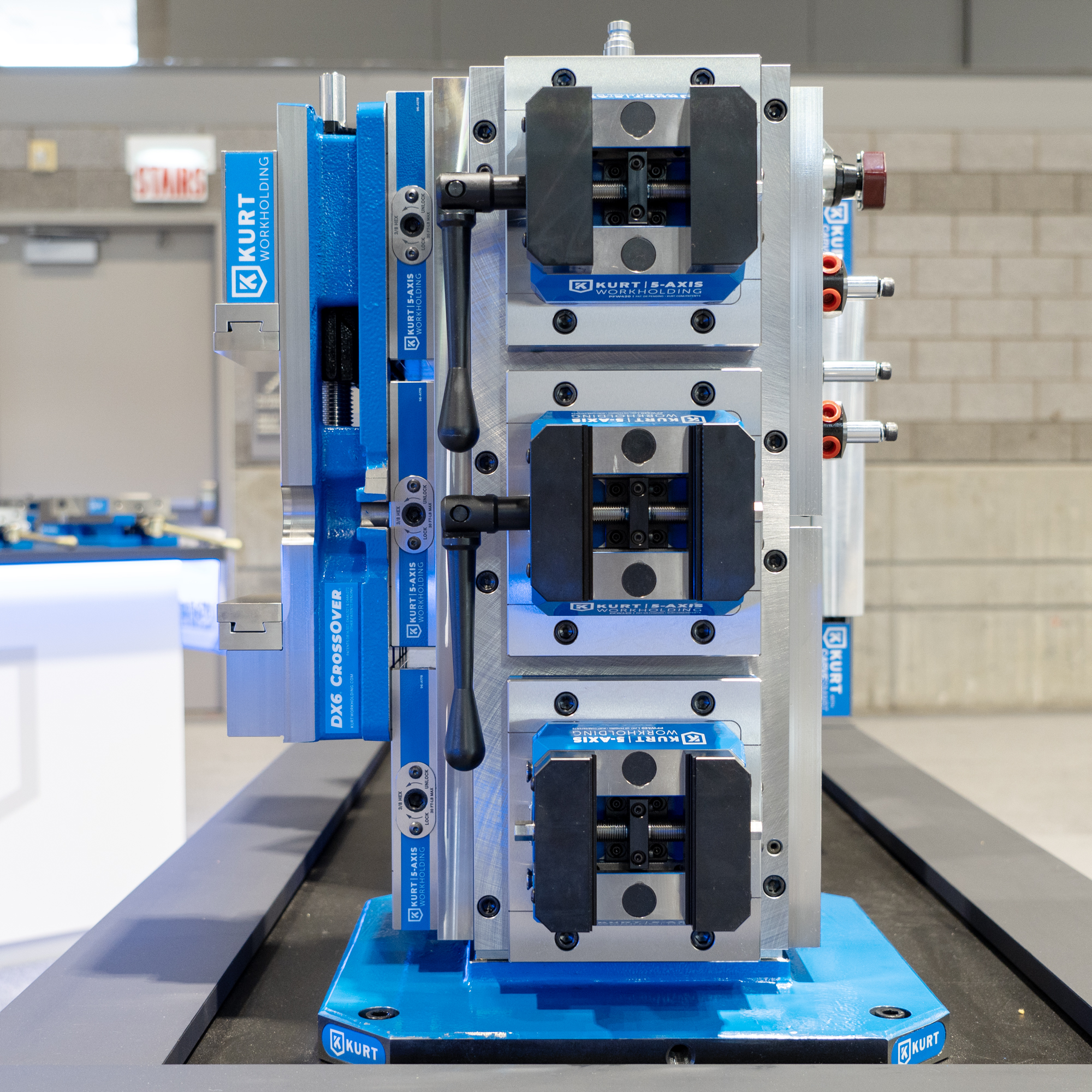
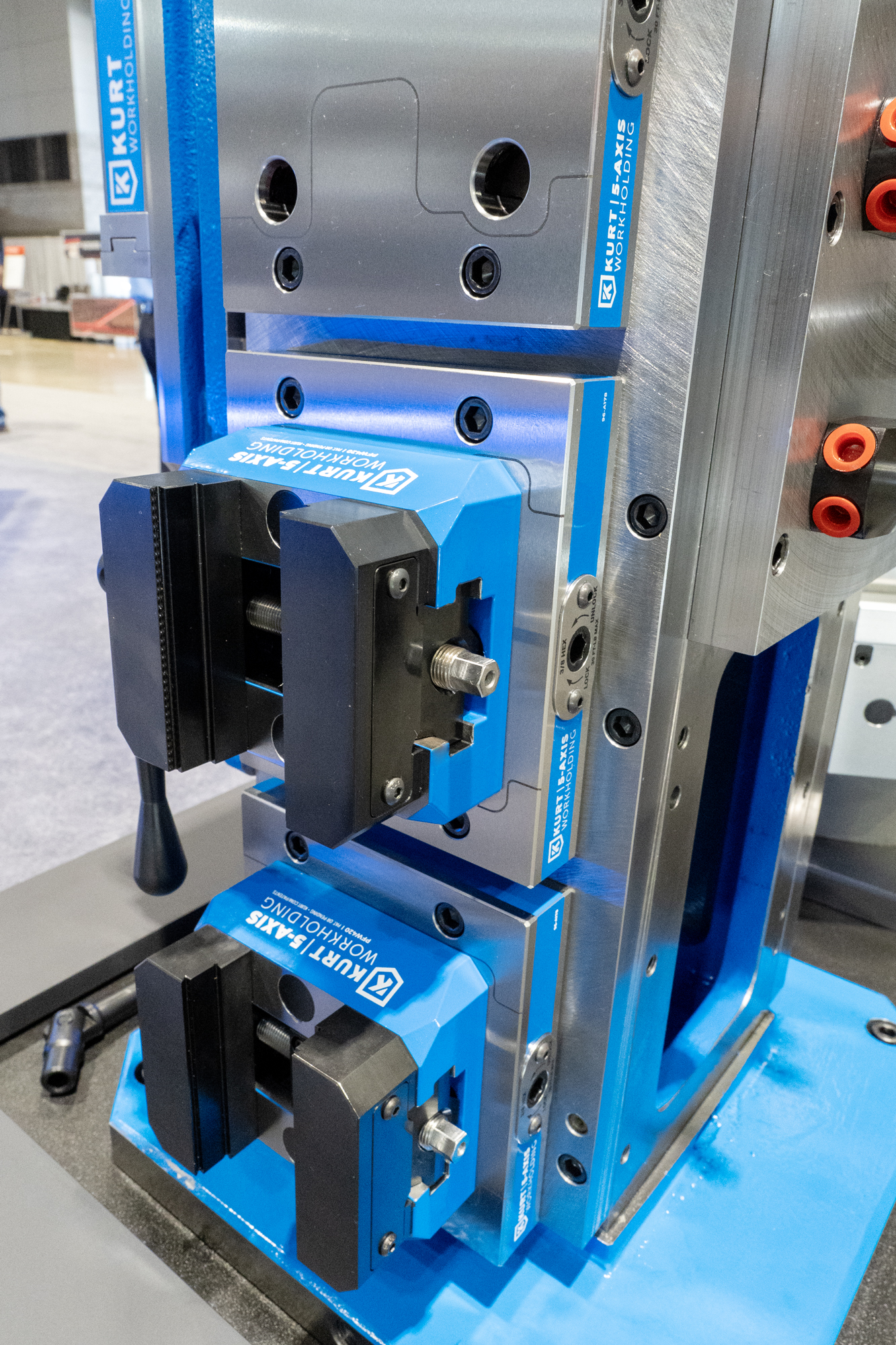
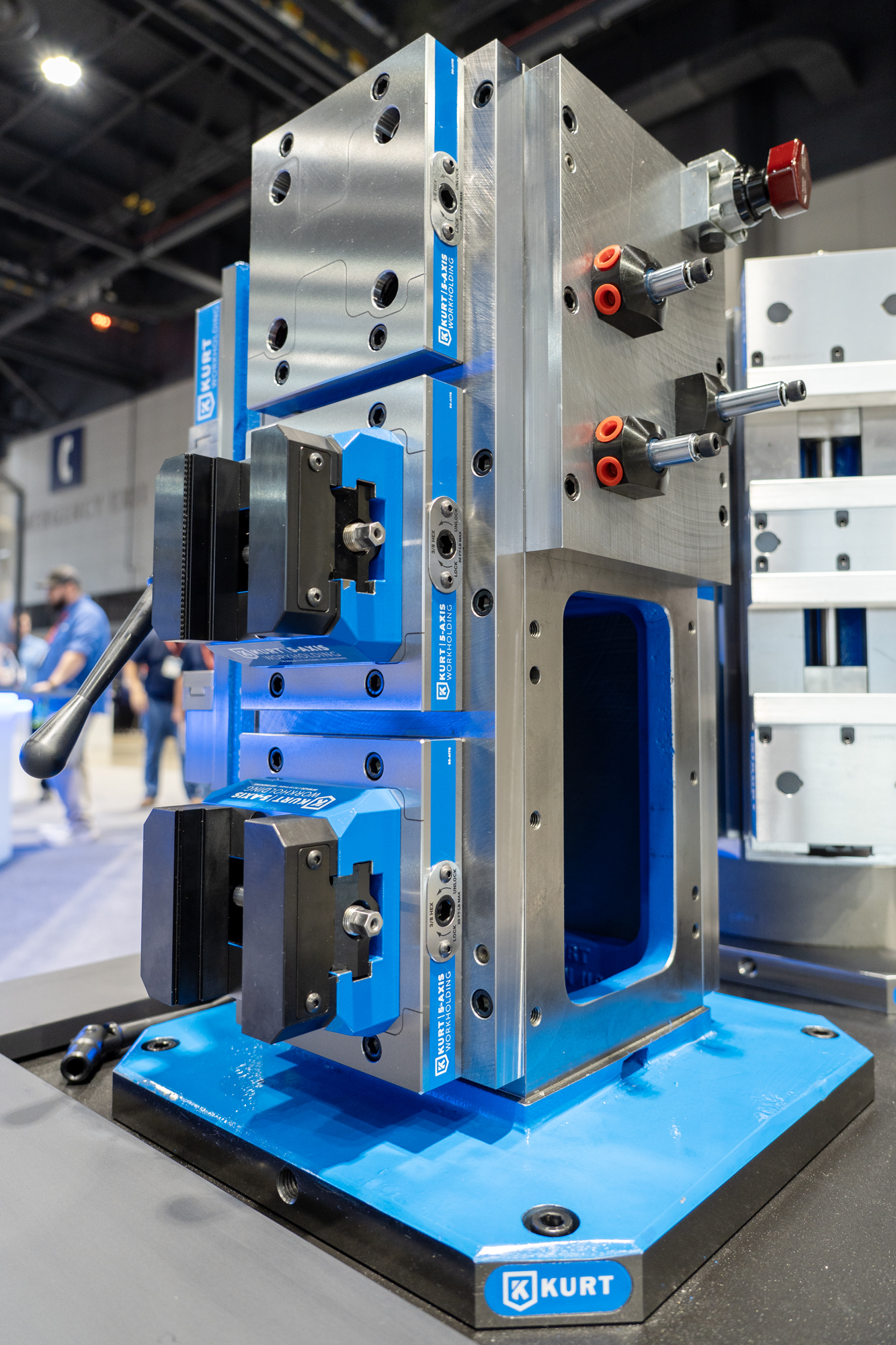
Have a look at the image gallery👆Everything from a hydraulic swing clamp system, to a DX6, to multiple PFW 5-axis and quick-change bases can be mounted to a single tombstone.
What Are Caged Tombstones?
Kurt’s caged tombstones feature 2 or 4 sides for mounting stock or custom workholding or fixturing. The hollow caged tombstone design is lighter than a standard tombstone and provides additional structure, rigidity, and vibration dampening when subplates are installed on each of the sides. Air and hydraulic lines and components can be concealed inside the tombstone, with easy access when subplates are removed.
While the caged design is great for hiding automation features, it can also maximize fixturing flexibility when used with multiple subplates and quick-change workholding like Kurt’s new receiver bases.
Key Caged Tombstone Features
- Multi-Face Design: 2-, 4-face configurations for versatility.
- Quick-Change Integration: Bolt-on subplates enable rapid tooling changeovers, reducing downtime.
- Optimized for Automation: Air and hydraulic lines can be routed internally and integrate tombstones with automated workholding and robotic machine tending systems.
- Flexible in a variety of applications: From pallet pools and Palletech FMS lines, to 2-pallet changers.
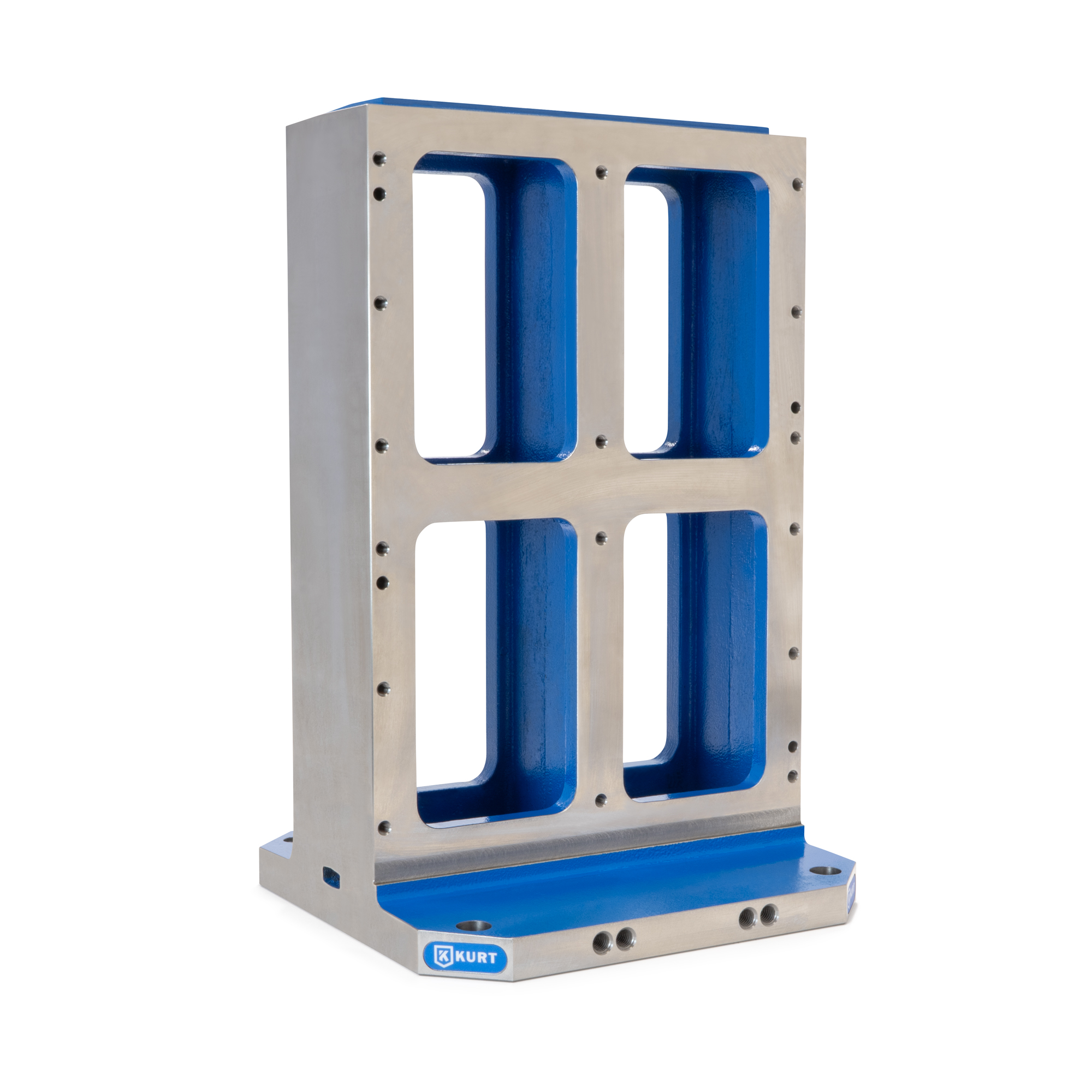
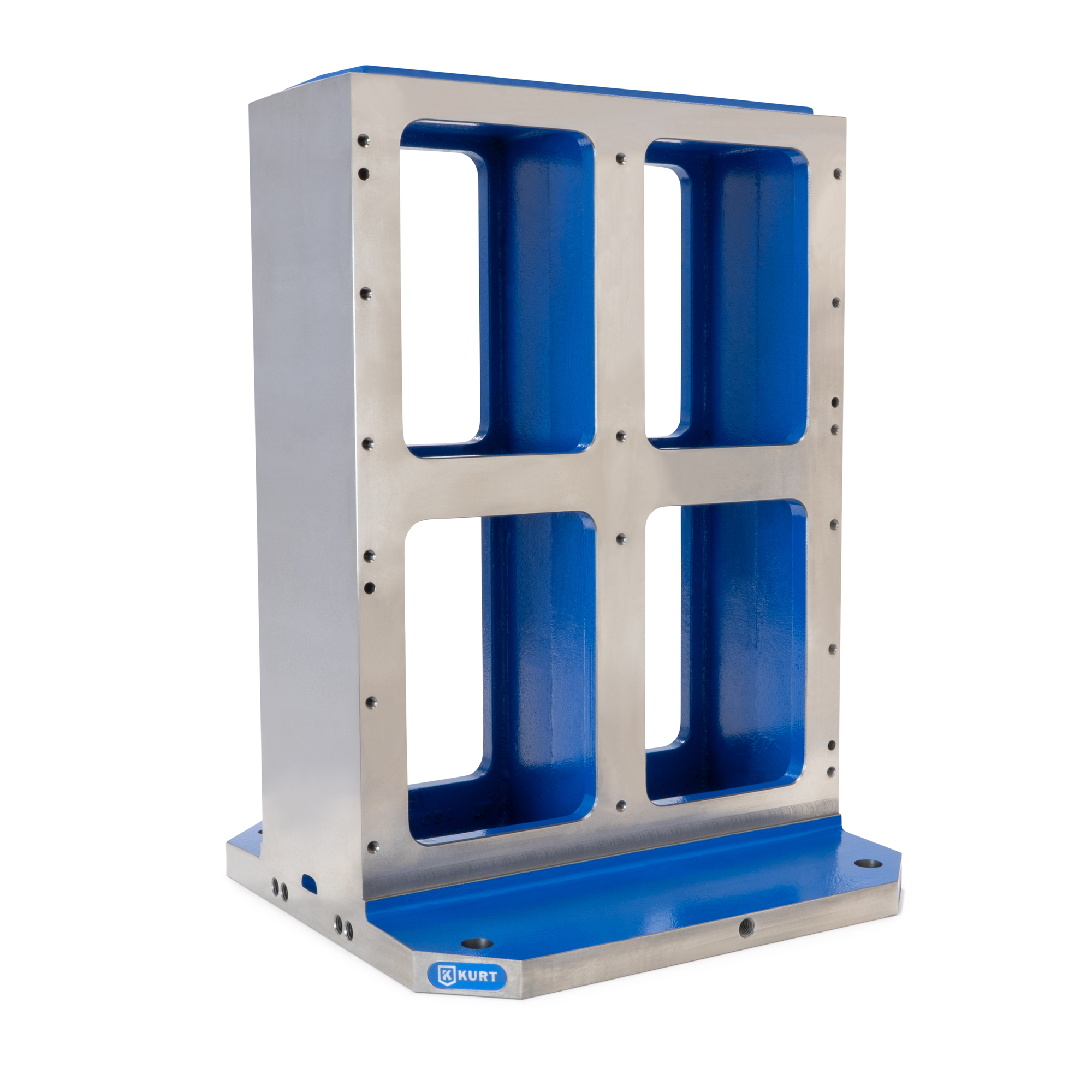

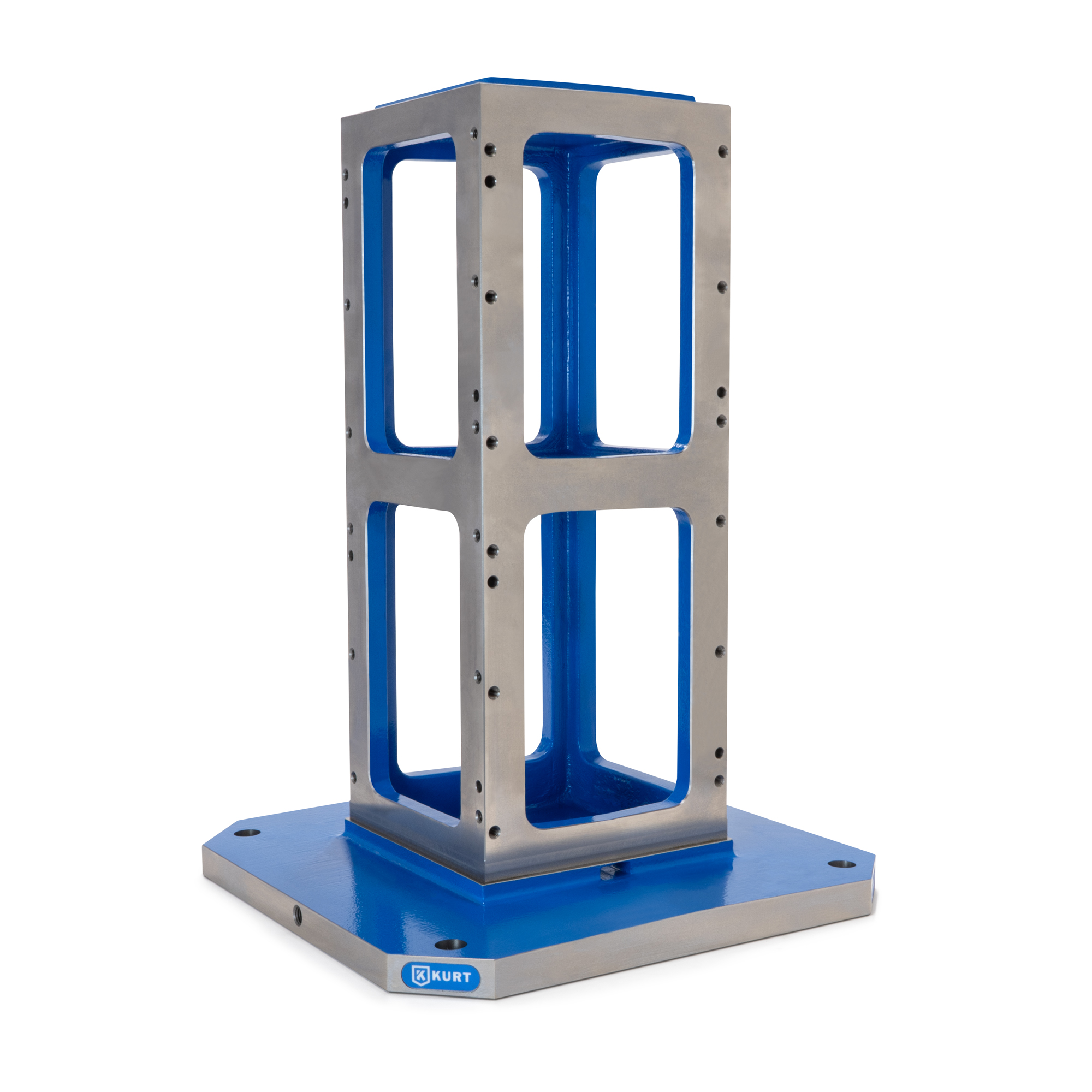
Benefits of Caged Tombstones in Machining Processes
1. Flexible Changeovers
Subplates are mounted over the open tombstone faces and can be changed much faster than swapping an entire tombstone. A tombstone can be “refixtured” with new subplates with new part setups in short order. Dowel pins ensure accurate subplate changeovers without sacrificing repeatability or delaying metal cutting. Quick-change receiver bases can further enhance caged tombstone flexibility.
2. Improved Efficiency
By holding multiple parts or part families simultaneously, caged tombstones significantly reduce setup times. Operators can machine several components in one cycle without the need for repositioning, drastically improving throughput.
3. High Tolerance Precision
The caged framework, with subplates bolted in place, reduces harmonic chatter. Less vibration helps with holding tight tolerances.
4. Maximized Machine Utilization
Multi-face configurations allow shops to take full advantage of horizontal machining center capabilities, enabling continuous machining on different sides of a part. This can help increase overall equipment efficiency.
5. Adaptability for Diverse Applications
Whether machining small or large parts, caged tombstones accommodate a wide range of sizes and materials and have become a staple in pallet pools, Palletech FMS lines and 2-pallet changers.
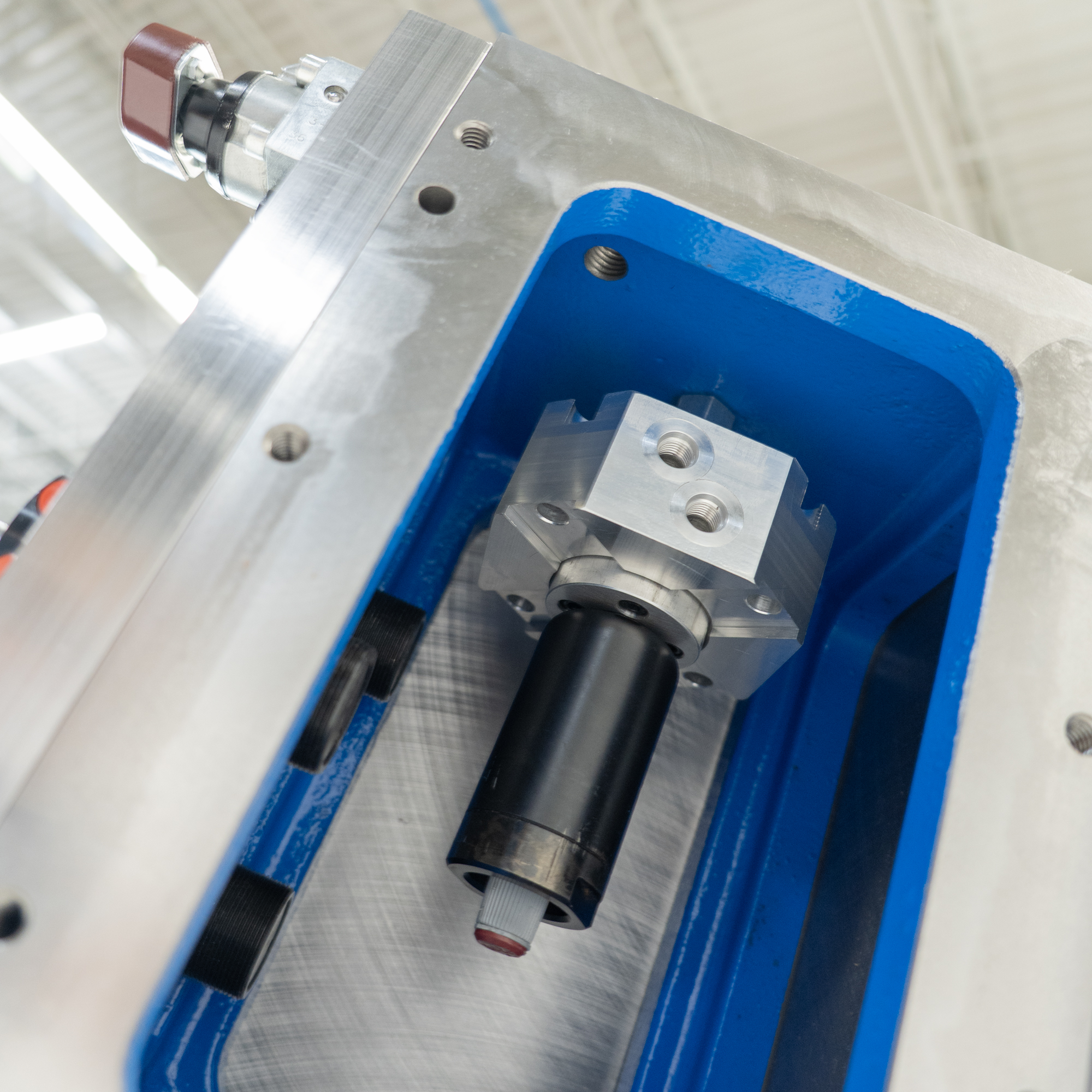
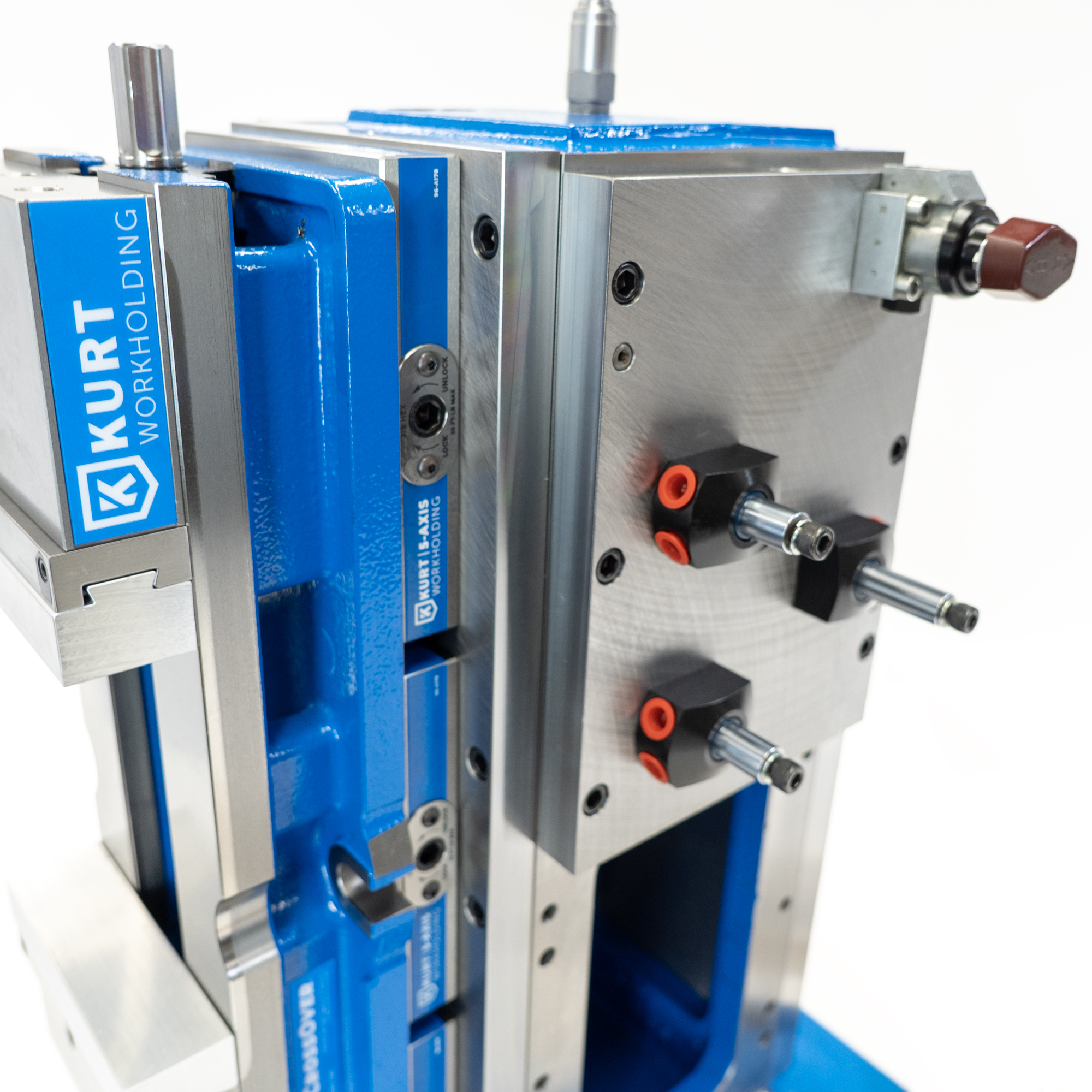
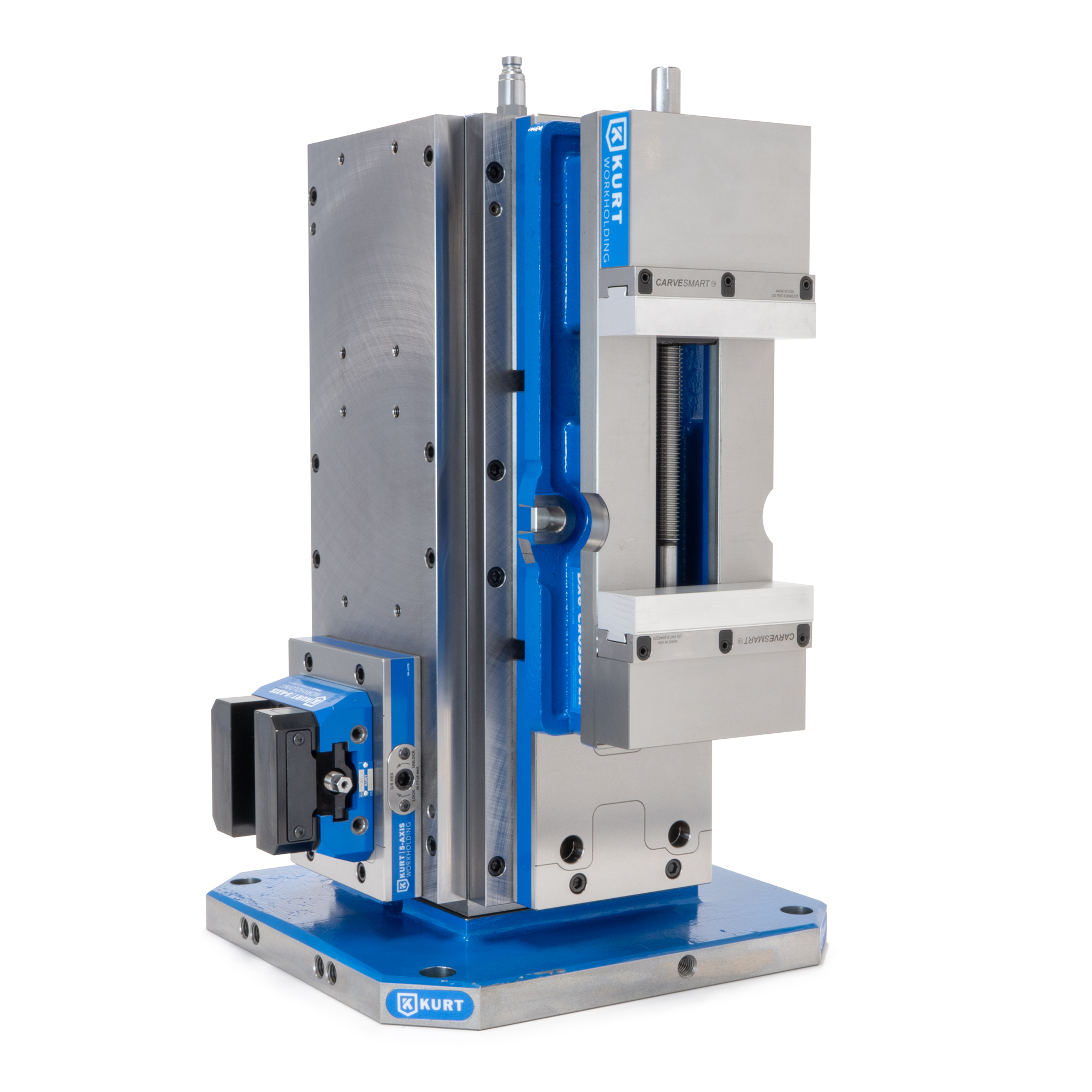
Invest in Precision and Performance
Caged tombstones are indispensable for manufacturers seeking reduced costs, increased productivity, and an edge on the competitive. Multi-face part holding will help shops streamline operations and deliver unparalleled precision—making them a must-have for any job shop or manufacturer looking to scale efficiently.
Need a Custom Tower or Tombstone?
You’ve come to the right place. If you can dream it up, Kurt’s Custom Workholding Team can create it for you. If you’re in need of an outside-the-box solution, describe your setup and tell us what you’re trying to achieve and we’ll put our creative team to work on it. Check out this example of a mega tombstone with XL6 extended vises and TriLock vises with Carvesmart jaws. –>
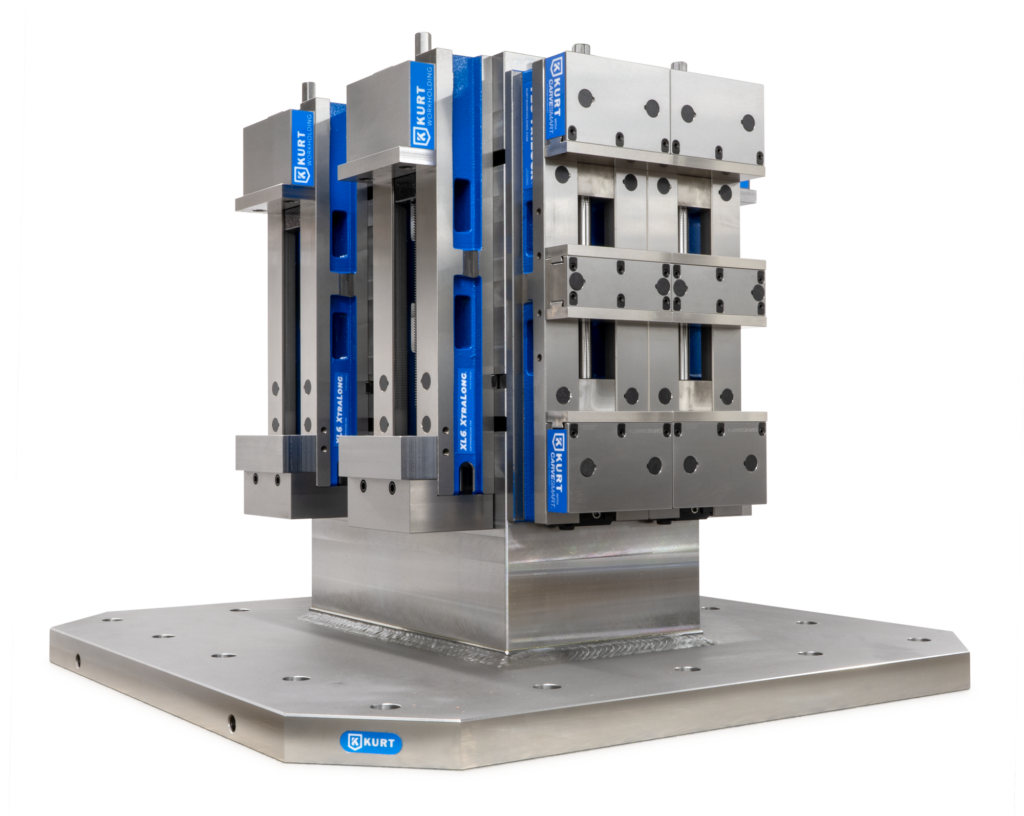