We’re shipping three new servo-driven vises for a new customer’s automation setup this month! A combination of off-the-shelf Kurt SCD640 self-centering 6-inch vises and Kinetix 5500 (Allen Bradley) servo motors controlled by a CompactLogix ERM is designed for robotic part and fixture changes and will be part of a Fanuc Robodrill Long bed Model E. Maruka USA is integrating the Fanuc Robodrill with the Kurt Workholding SCD640 Servo Vises for lights-out machining operation over a large family of parts.
Each vise is uniquely configured to handle a different part with custom jaws and fixturing. A cleverly designed drop-in fixture with magnets on the base is placed and removed by a robot and fits in the mounting bolt holes of the vise. The robot will deploy the fixture to balance and hold a part in place prior to vise-jaw closure.
“Servo vises run quietly, are better sealed from debris and aren’t susceptible to line contamination from dirty shop air or other supply-line issues.”
Click on the video to see the vise in action —>
Kurt Custom Engineered Servo vises make sense because they allow very granular control and more I/O options, including speed, torque and position outputs. The vises are programmed to open and close via the servo and to stall at a preset torque. The torque preset translates to a direct linear relationship between torque and force with our vises.
Servo drives also allow engineers to program a closed width for the part and a width slightly smaller than the part. This allows the machine to cycle off if there is no part in the vise and it hits the close width limit. When automating jaw opening and closing, servos are great for providing accurate high-resolution direct feedback for jaw position and motion.

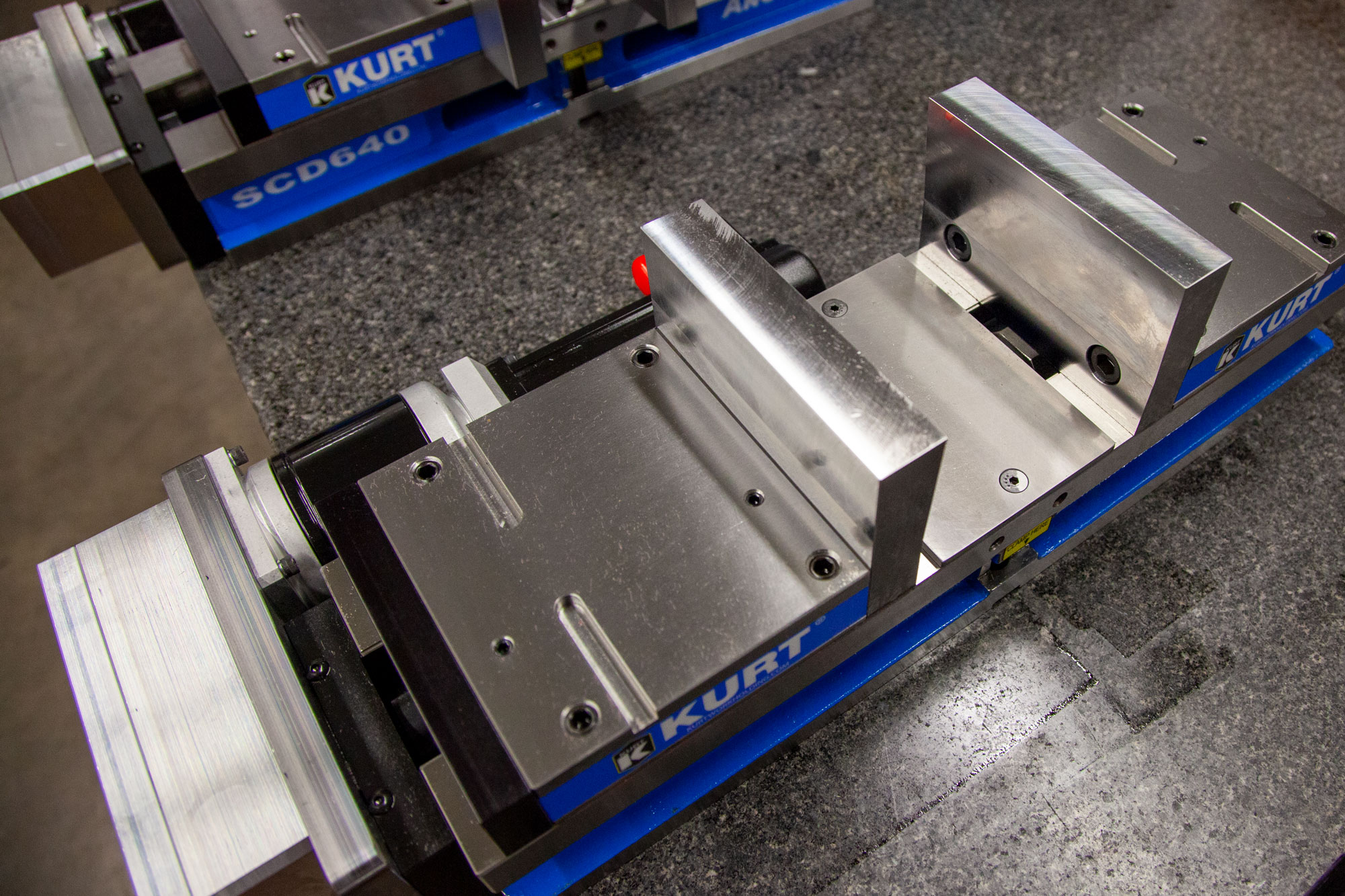
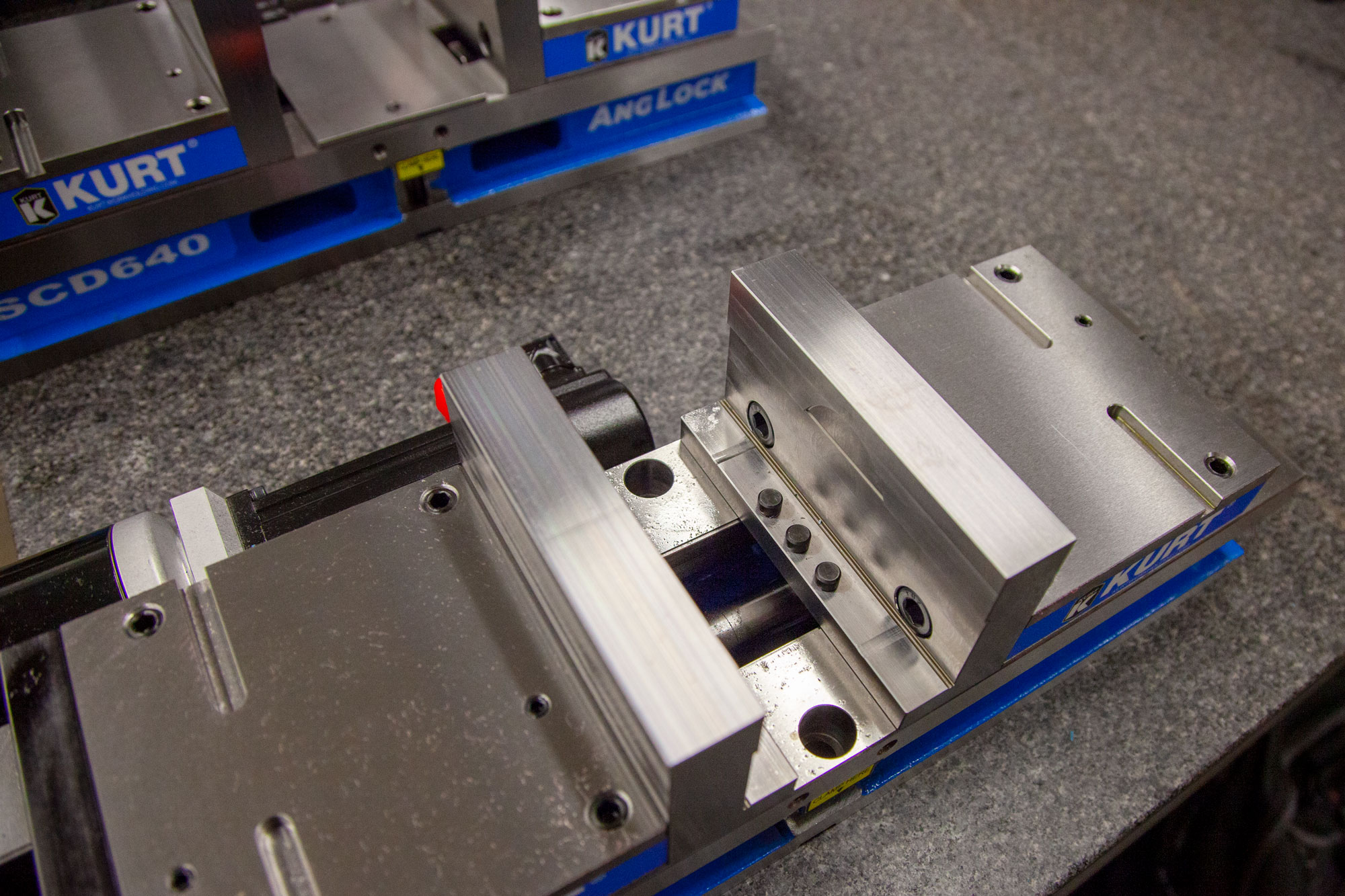
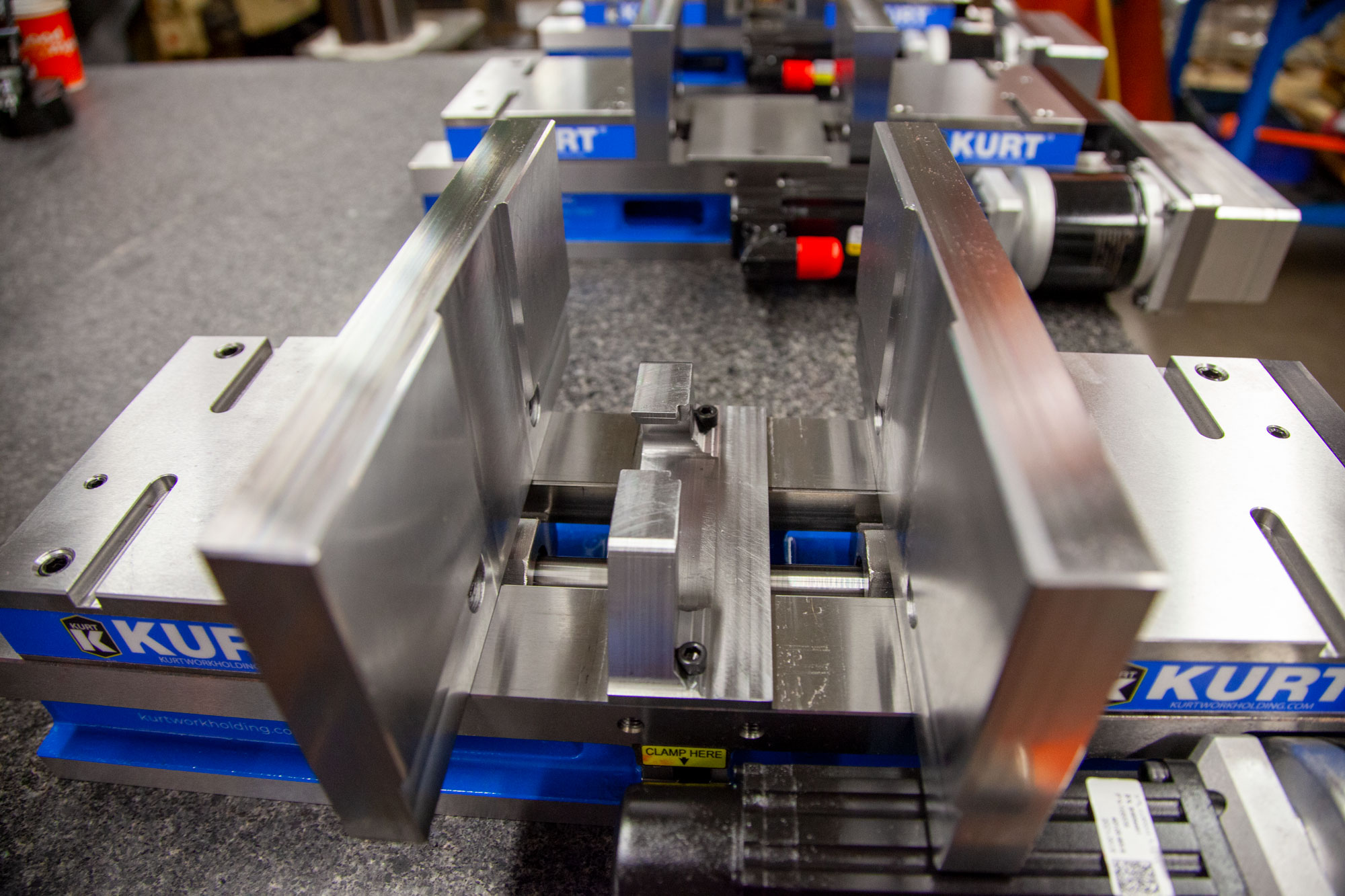
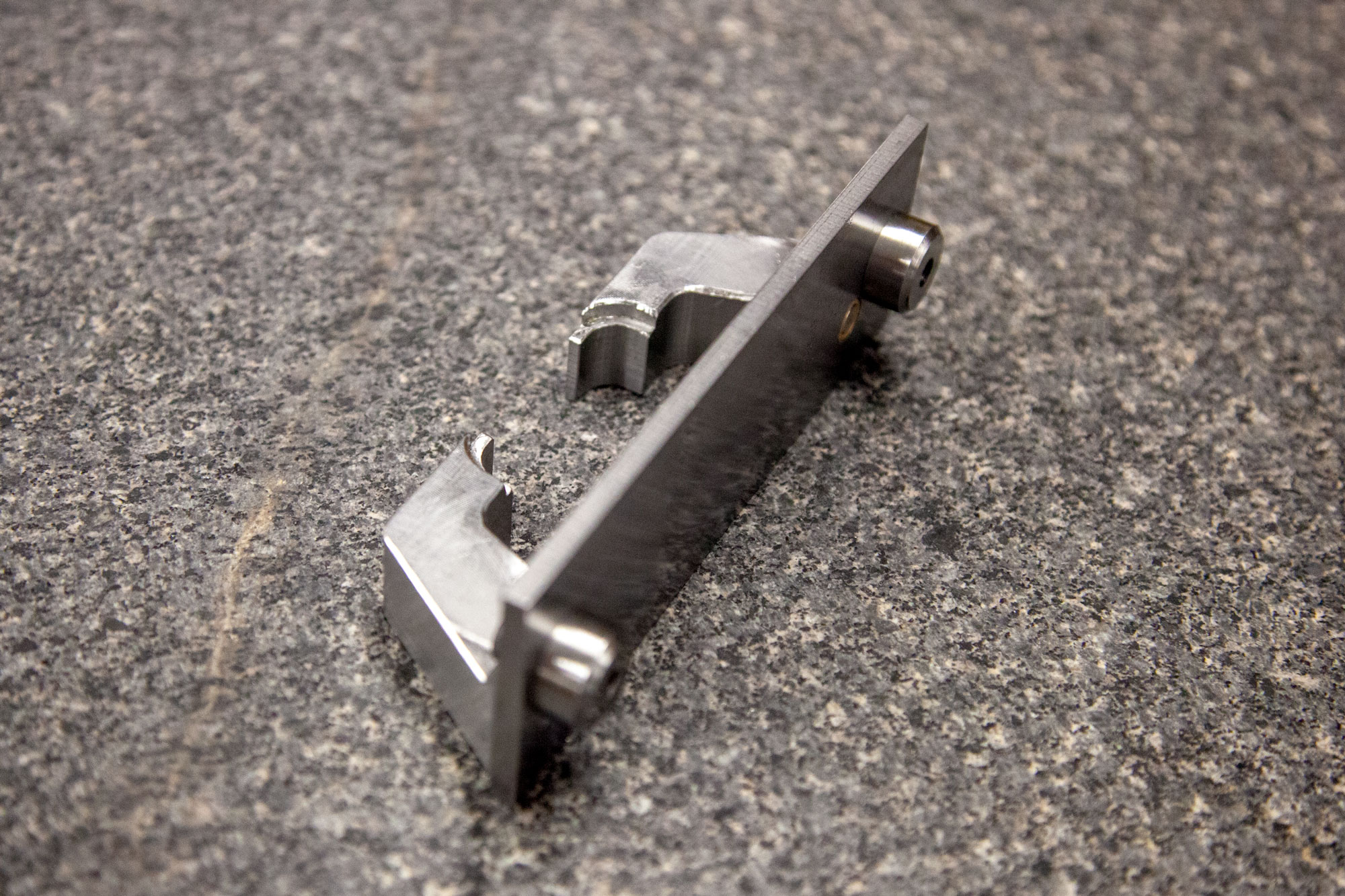
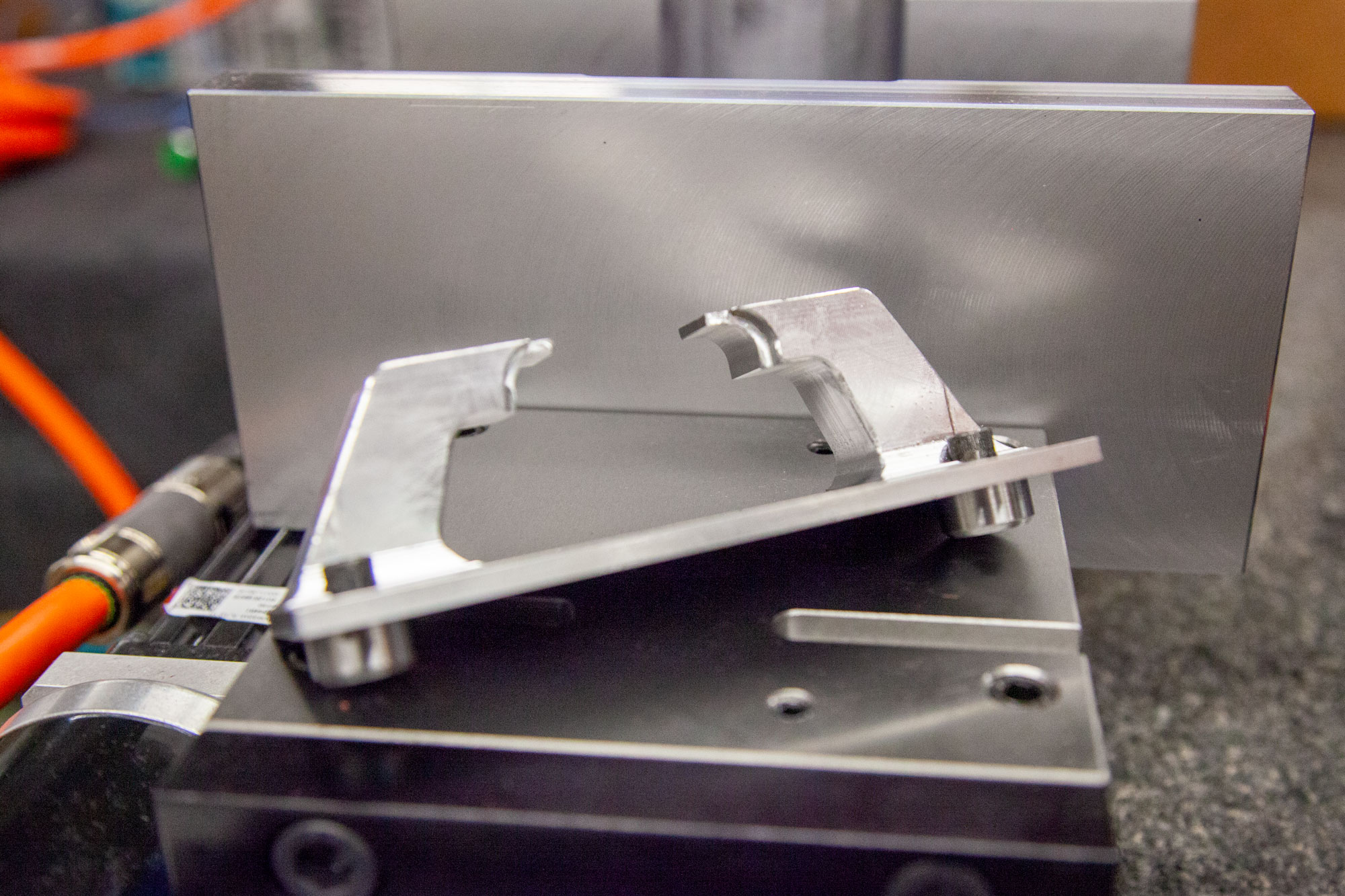
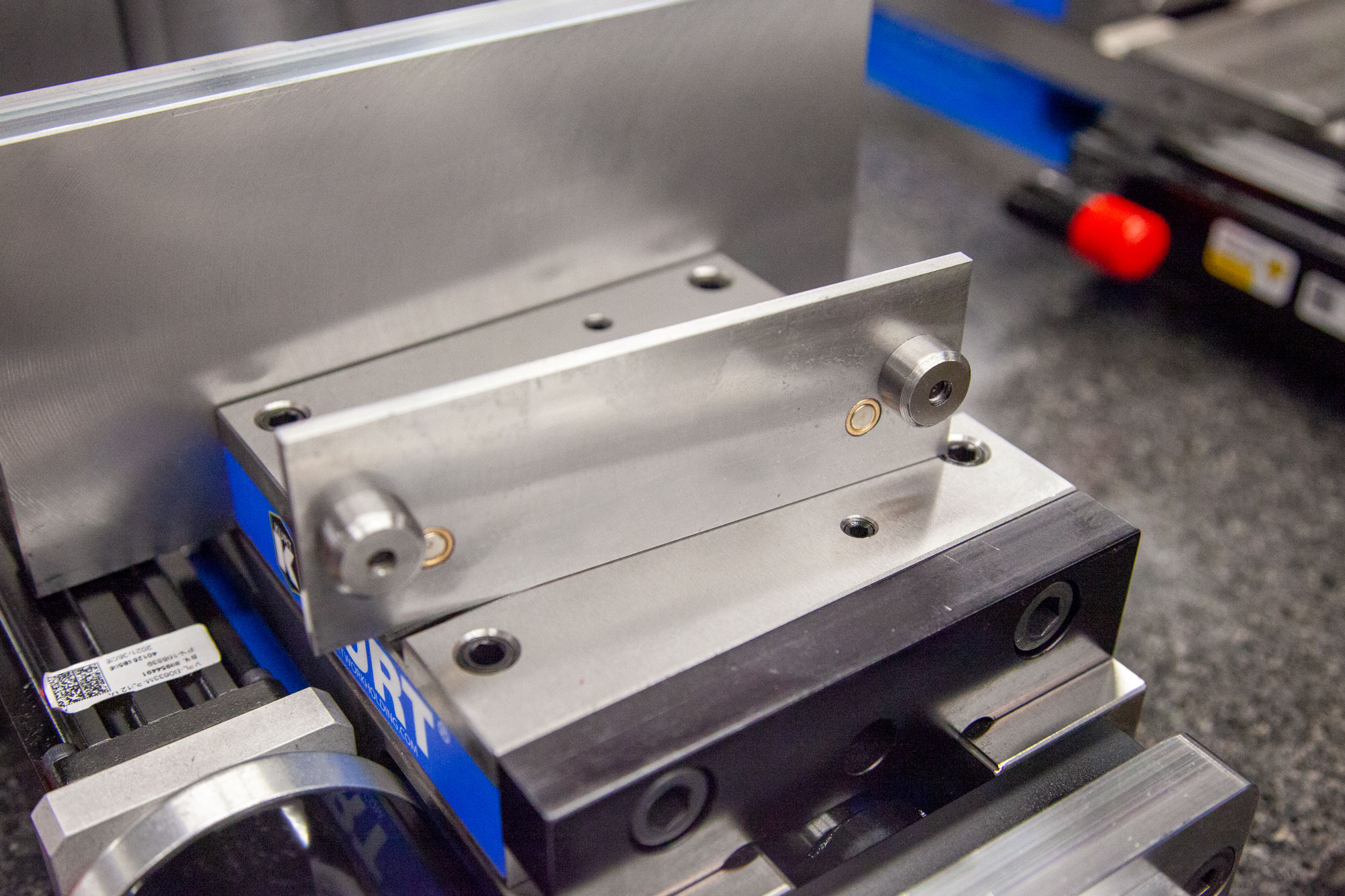
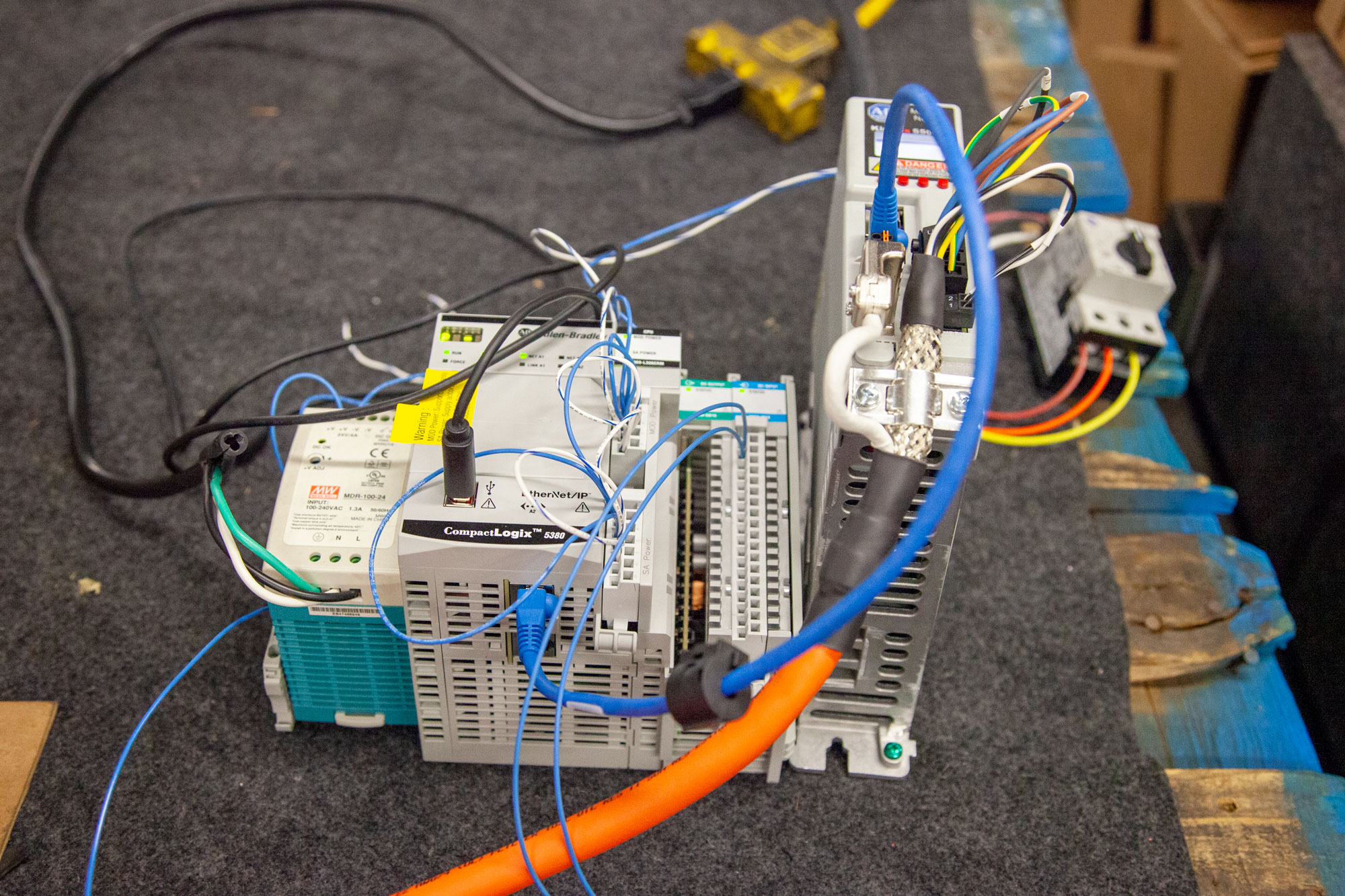
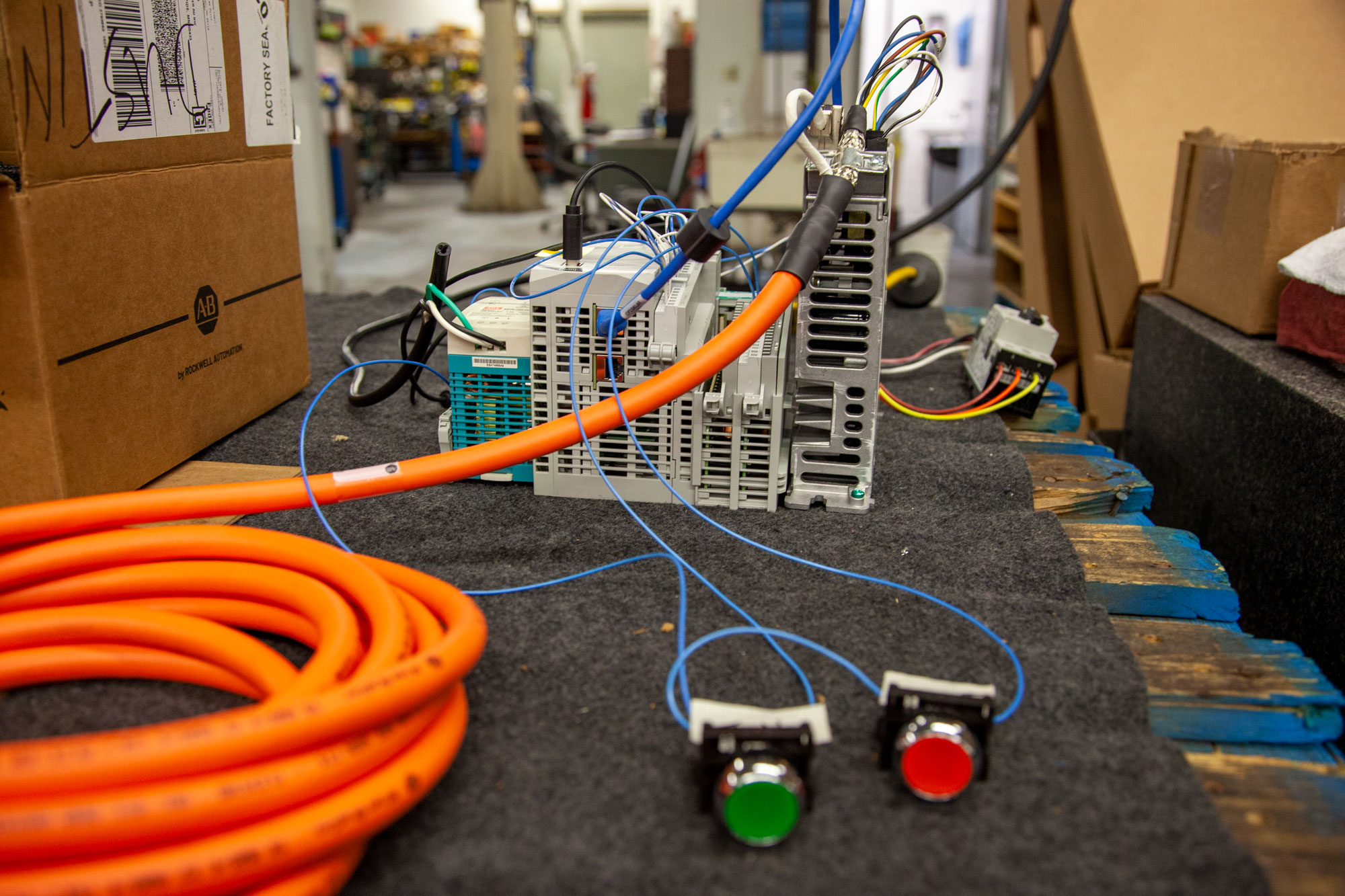
Why we used servo motors for this application:
- Servos allow greater control of clamping speed, torque and force needed to securely hold a part. This is especially important in a “light touch” application where you might deform or damage a part if the vise jaws come in too fast or with too much force.
- Servos are great for providing accurate high-resolution direct feedback for jaw position and motion when automating jaw open and close. Servos allow programmers to know that the jaw position is where they expect it to be—accurately and repeatably every time on each part cycle for a reliable vise automation system.
- Servos offer a lot of bang for the buck, achieving higher power output in a compact motor.
- Eliminating hydraulic or pneumatic lines in the machining environment helps clean up the setup and reduce clutter and maintenance around the milling machine.
- These motors also easily integrate into a control system that manages the machine-robot-workholding relationship including handshaking protocols and ladder logic—making for a more turn-key and easy-to-program setup for the end customer.
- Finally, we find that servo motors perform well in a shop environment where they run quieter than hydraulic and pneumatic setups, are better sealed from debris and aren’t susceptible to line contamination by dirty shop air or other issues associated with supply lines.
If you’re interested in applying a similar automation system to a custom engineered workholding application or learning how we can streamline an automated workflow, we’d love to help you out. We can build virtually anything imaginable.
Send us some project details and we’ll get back to you with the solution that’s right for your budget and your application.