Kurt offers a broad range of custom gaging solutions for the food and beverage industries and can modify them for any customer needs.
Back-end Flange/Neck Gage
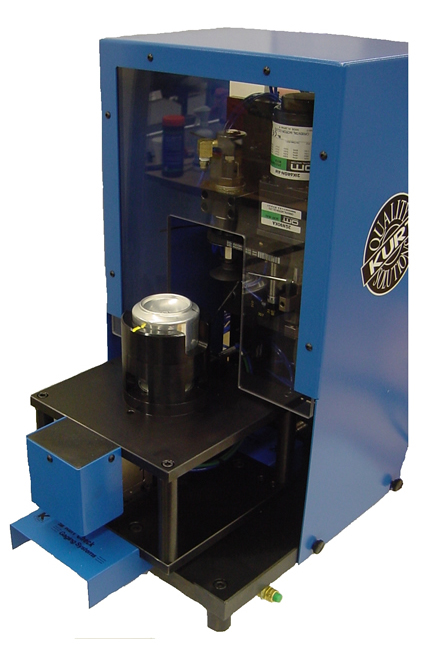
The manually loaded Kurt Back-end Flange/Neck Gage measures the “Finished Can Height”, the “Flange Width” and the “Neck Plug” Diameter of beverage and/or food cans as may be applicable. The gage station uses a sleeve type nest that captures the OD of the can. The Kurt Back-end Flange/Neck Gage can measure multiple can heights in a single gage station as long as the OD is the same. Changeover from one length can to another can take place within a few minutes. A single gage can also accommodate two neck plug sizes; changeover from one neck plug size to another is accomplished with the flip of a switch. The gage measures the features as displayed on the can image.
To measure a can the following sequence takes place:
- The beverage can is manually loaded into a sleeve type nest that captures the OD of the can with the opening of the can facing down
- Once the can to be measured is in place, two start/stop buttons are actuated and the can is moved back into a measurement position
- Once the can is in the measurement position, a vacuum drive system engages the can on the dome and begins to rotate the can
- Measuring heads are extended to capture the features outlined
The data output can be made available to many available software data collection systems. The speed of data collection and processing is a function of those software packages
When the gage is used with KurtSPC Data Collection the information from the can gage is recorded and visually depicted:
- During rotation, data is gathered at 250 readings per second
- During full can rotation of about 4 seconds, 1000 readings around the can at each location are recorded
- The KurtSPC software provides MINimum, MAXimum and AVErage results as shown
- The KurtSPC software can also provide a visual depiction of the can profile as shown
The Kurt Back-end Flange/Neck Gage can be set-up to measure various can lengths on a single gage station provided the can ID is the same. The Kurt Back-end Flange/Neck Gage will accommodate different size flange widths and with the flip of a pneumatic switch can measure between two different can Neck Plug sizes. Changeover from one can size to another is accomplished in 5 minutes or less. The Kurt Back-end Flange/Neck Gage can be built to measure virtually any size beverage or food can. Gage cycle time to collect information for 1 can is approximately 8 seconds. A master is required with the gage station for each size can
Beverage/Food Can Burst (Dome Reversal) Gage
The Kurt Can Burst Gage Station can be used in a manually loaded gage station our in a fully automated line. The Burst Gage Station will apply pressure force inside a beverage can to determine the Burst (or Dome Reversal) strength of the can. The Beverage Can is located on a nest within the gage in an upright position; the open end of the finished can is down. Once in position, the flanged portion of the can is sealed and the beverage can is held in position. The Burst cycle is started and an increasing pressure force is applied inside the can. A pressure sensor is used to continually monitor the pressure applied and will determine and record the maximum load applied when the failure point as the can dome is reversed.
To measure a can the following sequence takes place:
- The beverage can is manually or robotically loaded into a part type nest that captures the ID of the finished beverage can neck; the can opening is facing down
- Once the can to be measured is in place, two start/stop buttons on the manually gage or the automatic start in an auto gage is actuated and the Burst cycle begins
- The beverage can is immediately sealed at the bottom and restrained from movement
- Pressure is slowly increased inside the can and recorded dynamically
- The pressure sensor is dynamically monitored at 200 readings per second to capture the maximum Burst pressure
The data output can be made available to many available software data collection systems. The speed of data collection and processing is a function of those software packages
When the gage is used with KurtSPC Data Collection the information from the can gage is recorded and visually depicted:
- During the crush cycle, data is gathered at 200 readings per second
- The Burst Gage Station can include an LVDT pencil probe that is used to measure the dome height
- Pressure can be applied at 90psi and held (or some other desired reading) and the dome height can be measured before pressure is again applied to actually reverse the dome
- Full Burst cycle may take up to 10 seconds
- The KurtSPC software captures the maximum pressure value recorded
The pressure sensor utilized in the Burst Gage is calibrated and certified to NIST standards
Beverage/Food Can Crush Gage
The Kurt Can Crush Gage Station can be used in a manually loaded gage station our in a fully automated line. The Crush Gage Station will apply crush force to the can in a vertical direction to determine the crush strength of the can. The Beverage Can is located on a nest within the gage in an upright position; the open end of the finished can is down. Once in position, the gage cycle is started and an increasing pressure force is applied to the can. A pressure sensor is used to continually monitor the force applied and will determine and record the maximum load applied when the failure point as the can buckles is attained.
To measure a can the following sequence takes place:
- The beverage can is manually or robotically loaded into a part type nest that captures the ID of the finished beverage can neck; the can opening is facing down
- Once the can to be measured is in place, two start/stop buttons on the manually gage or the automatic start in an auto gage is actuated and the crush cycle begins
- The pressure sensor is dynamically monitored at 200 readings per second to capture the maximum crush pressure
The data output can be made available to many available software data collection systems. The speed of data collection and processing is a function of those software packages
When the gage is used with KurtSPC Data Collection the information from the can gage is recorded and visually depicted:
- During the crush cycle, data is gathered at 200 readings per second
- Full crush cycle may take up to 10 seconds
- The KurtSPC software captures the maximum pressure value recorded
The pressure sensor utilized within the Crush Gage is calibrated and certified to NIST standards
Front-end Wall Thickness Gage
The manually loaded Kurt Front-end Wall Thickness Gage will measure the ‘Thin Wall’ and ‘Thick Wall’ dimensions of beverage or food cans. The gage measures the features at the locations as shown in the image. The Kurt Wall Thickness gage can measure multiple length cans on a single gage as long as the ID of the cans is the same. Changeover from one can length to another can be done within a few minutes.
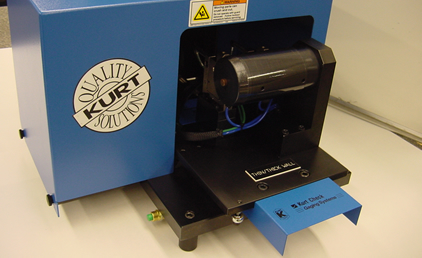
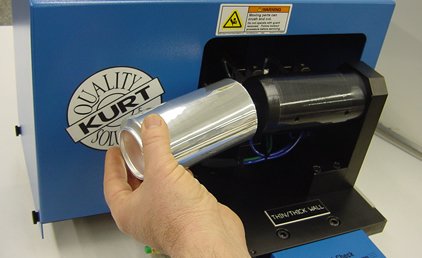
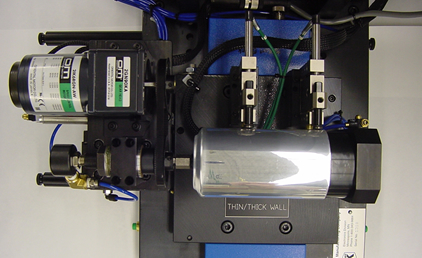
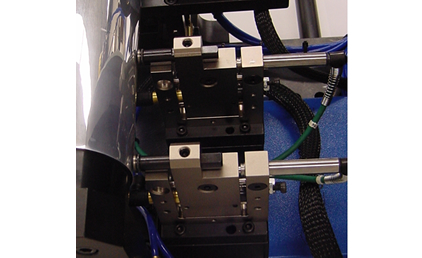
To actually measure a part the following sequence takes place:
- The beverage can is manually loaded over a mandrel that replicates the can ID size.
- Once the can to be measured is in place, two start/stop buttons are actuated and the can is moved back into a measurement position
- Once the can is in the measurement position, a vacuum drive system engages the can and begins to rotate the can about the mandrel
- LVDT pencil probes are extended and measure the can wall thickness as the can is rotated
The data output can be made available to many available software data collection systems. The speed of data collection and processing is a function of those software packages
When the gage is used with KurtSPC Data Collection the information from the can gage is recorded and visually depicted
- During rotation, data is gathered at 250 readings per second
- During full can rotation of about 4 seconds, 1000 readings around the can at each location are recorded
- The KurtSPC software provides MINimum, MAXimum and AVErage results as shown
- The KurtSPC software can also provide a visual depiction of the can profile as shown
The Wall Thickness gage can be set-up to measure various can lengths on a single gage station provided the can ID is the same. The Wall Thickness gage can be built to measure virtually any size beverage or food can. Gage cycle time to collect information for 1 can is approximately 8 seconds
No master is required with the gage station
Front-end Trim/Dome Gage
The manually loaded Kurt Front-end Trim/Dome Gage measures the “Trim Height” and the “Dome Depth” of beverage and food cans as may be applicable. The gage station uses a sleeve type nest that captures the OD of the can. The Kurt Trim/Dome gage can measure multiple length cans in a single gage as long as the OD is the same. Changeover from one length can length to another length can take place within a few minutes. The gage measures the features as displayed on the can image.
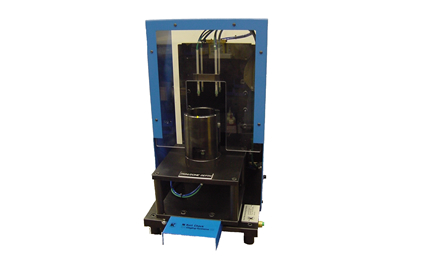
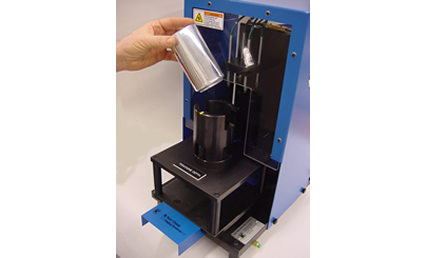
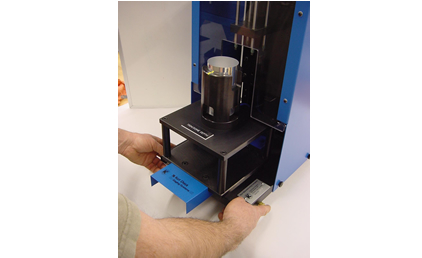
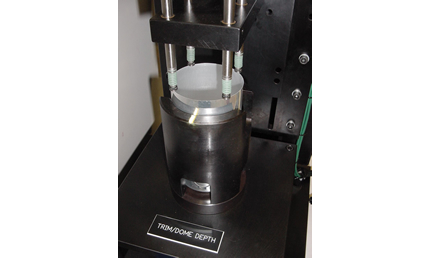
To measure a can the following sequence takes place:
- The beverage can is manually loaded into a sleeve type nest that captures the OD of the can with the open end of the can facing up
- Once the can to be measured is in place, two start/stop buttons are actuated and the can is moved back into a measurement position
- Once the can is in the measurement position, four LVDT pencil probes are extended to touch the trimmed top of the can and a single probe is extended to measure the dome depth
- The four probes on the top of the can measure the Trim Height of the can while the single probe on the bottom captures the dome depth
- The Trim Height probes are located as depicted at 0, 90, 180 and 270 degrees around the can
The data output can be made available to many available software data collection systems. The speed of data collection and processing is a function of those software packages
When the gage is used with KurtSPC Data Collection the information from the Kurt Trim/Dome can gage is recorded and visually depicted:
- The KurtSPC software provides MINimum, MAXimum and AVErage results as shown
- The KurtSPC software can also provide a visual depiction of the can profile as shown
The Wall Thickness gage can be set-up to measure various can lengths on a single gage station provided the can ID is the same. The Wall Thickness gage can be built to measure virtually any size beverage or food can. Gage cycle time to collect information for 1 can is approximately 5 seconds
A master is required with the gage station for each size can