Pin-point precision. All-around impressive.
Kurt didn’t just become the leading manufacturer of custom quality solutions overnight. We’ve spent the last 40 years thinking, creating and refining our process and products to make them perfect for you.
Why trust Kurt’s tailor-made precision gaging equipment? For starters, it improves quality control and production throughput to provide true ROI. It’s why our clients continue to use Kurt for all their custom quality solutions.
Our Quality Clients
From automotive manufacturers to tier-one subcontractors who manufacture components and assemblies, Kurt clients span most areas of precision manufacturing. Kurt Gaging also provides SPC software/hardware solutions and probes to OEM gaging/fixture makers and robotic system integrators.
Kurt Gaging Solutions
Kurt Workholding offers a variety of custom and standard gaging solutions for a range of industries. Explore the links to learn more about our capabilities and gaging solutions.
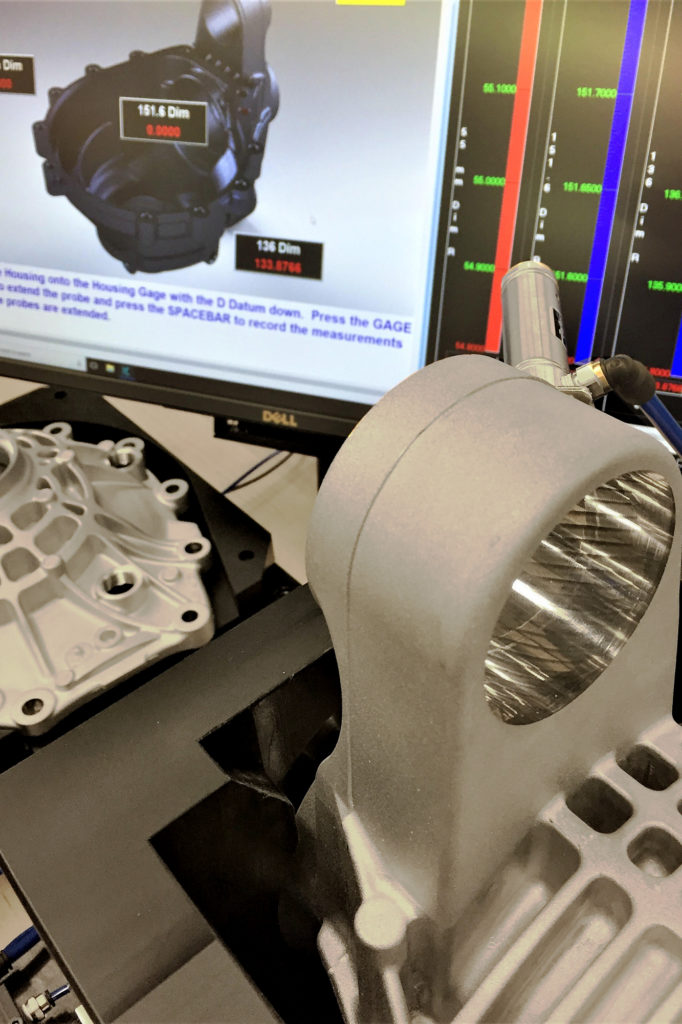
Technologies Used
- Vision contact/non-contact
- LVDT contact displacement sensors
- Laser-spot/measurement/profile
- 3D measurement
- Load cells
- Bar code scanning
- Generating
Our Gaging Systems
Kurt Gaging Systems build a variety of multi-dimensional gaging systems:
Manual Benchtop Gages
For off-line sampling and statistical analysis of the data.
SPC Benches
Provides a step-by-step sequence for the operator using a variety of hand-held gaging and statistical analysis of the data — reducing errors and time-consuming manual-data entry.
Automatic Integrated Gages
Increase production with closed-loop feedback gaging. Features precision controls of the workpiece in harsh shop environments with statistical analysis of the data.
We provide excellent “service after the sale.” Phone support, documentation, annual calibrations and regular SPC-training classes all combine to build long-term partnerships with clients and to keep their gaging system operating accurately for years.
Project Highlights
Automotive Application — Rocker Arms
Each part was fed into the gage via a vibratory rail type in-feed system with rejected parts guided down disposition chutes.
- 1 part every 3.6 seconds/Cycle 4 parts at a time
- 12 different critical dimensions 3 attribute checks
- Tolerance +/- 0.003mm
- Clamping the part on a 3-point datum
- All features under 10% GR&R
- Custom SPC data report
Post-Process Control Gaging Systems
Our post-process control gaging systems feature closed loop control in conjunction with 3rd party auto comp systems.
Pick-to-Light Systems
Help your team see the light. Our pick-to-light systems are an error proofing system for reducing errors and defects in quality/production processes. Lights direct operators to the correct parts, in the correct sequential steps this process also eliminates wasted touches common to paper-based handling.
Certified Calibration Masters
A master duplicates dimensional shapes of the parts to be inspected for use in zero setting. Our masters are certified and come with a heavy shipping case for protection in the shop environment — special material types, hardness and coatings are available upon request.
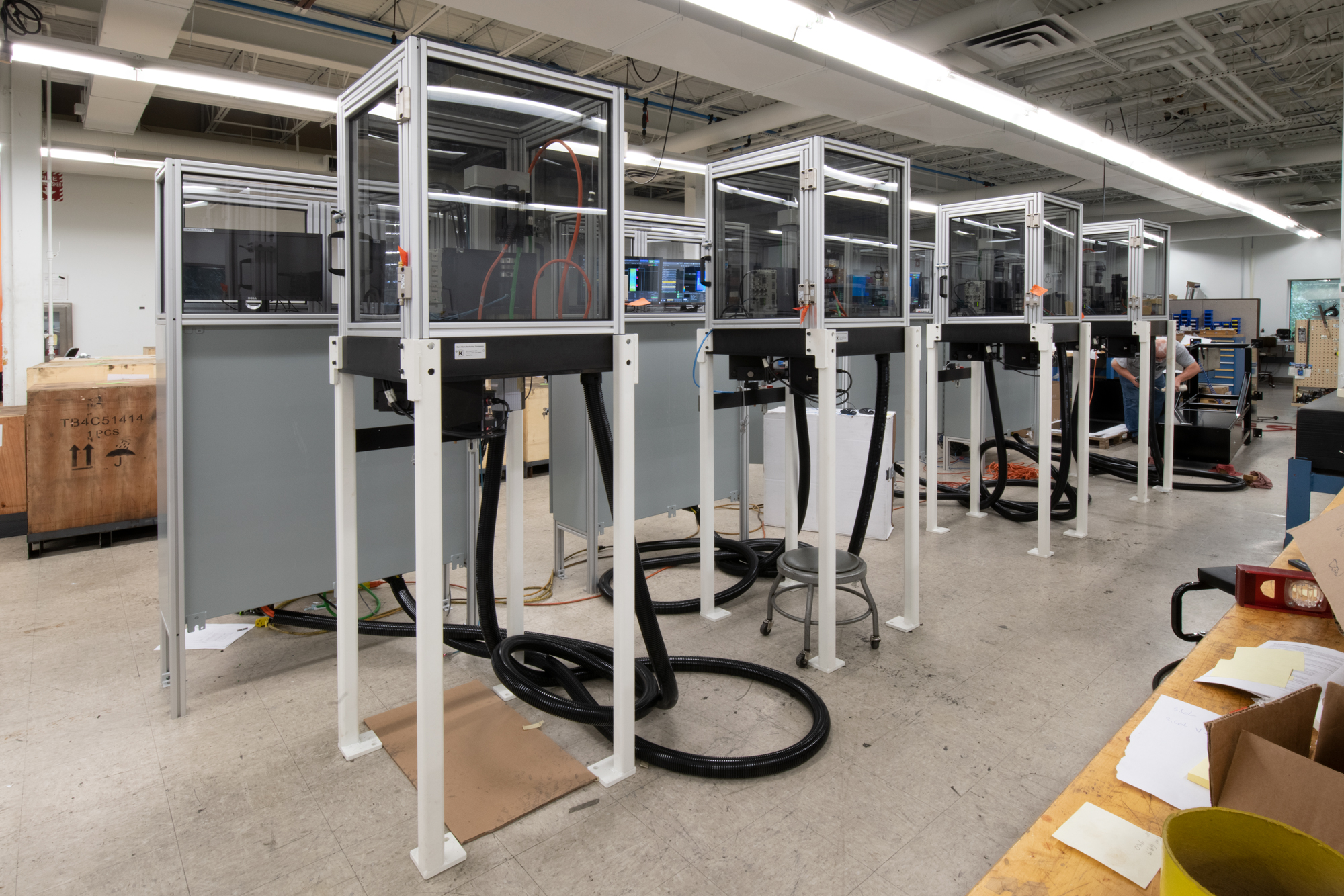
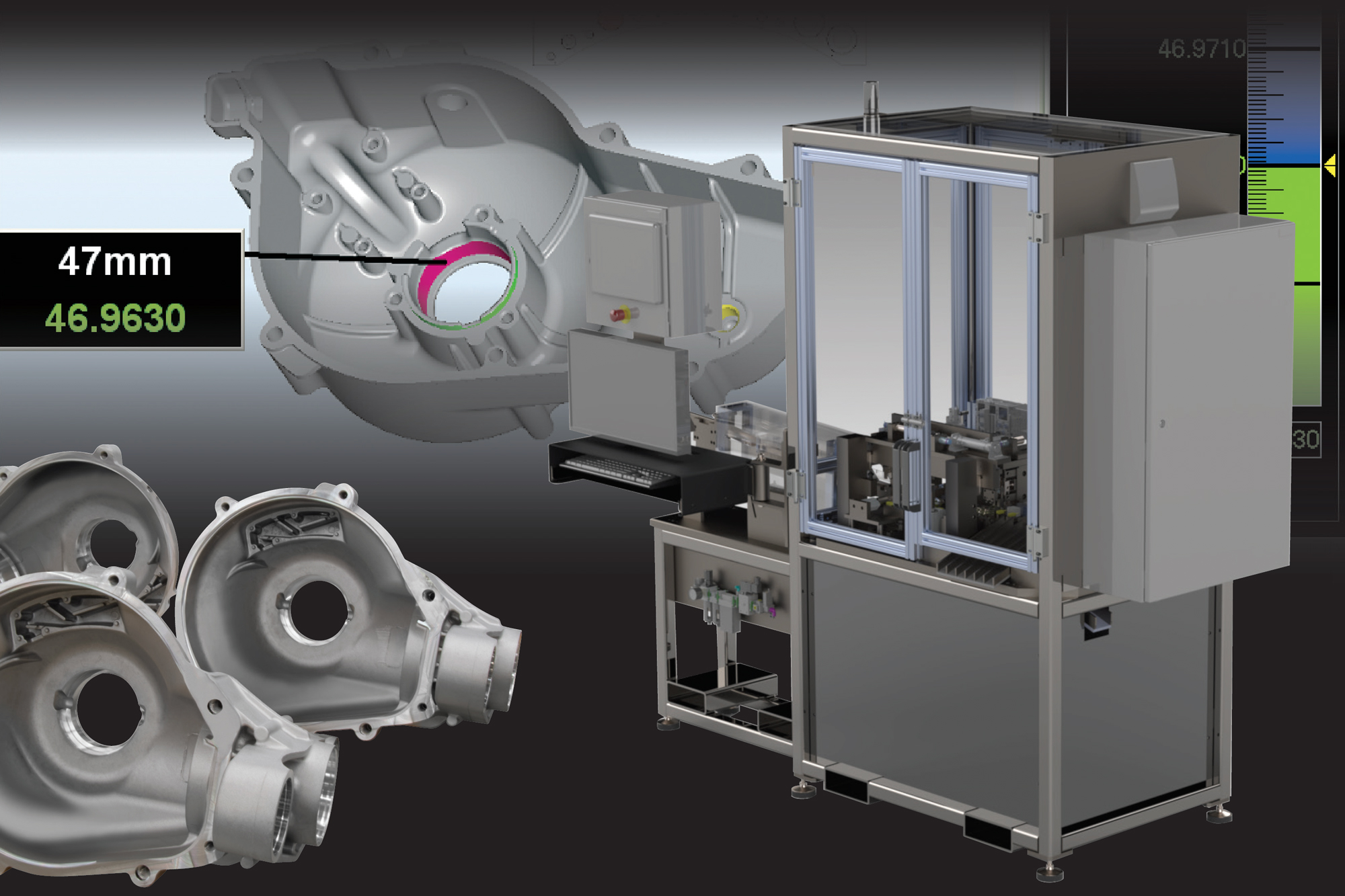
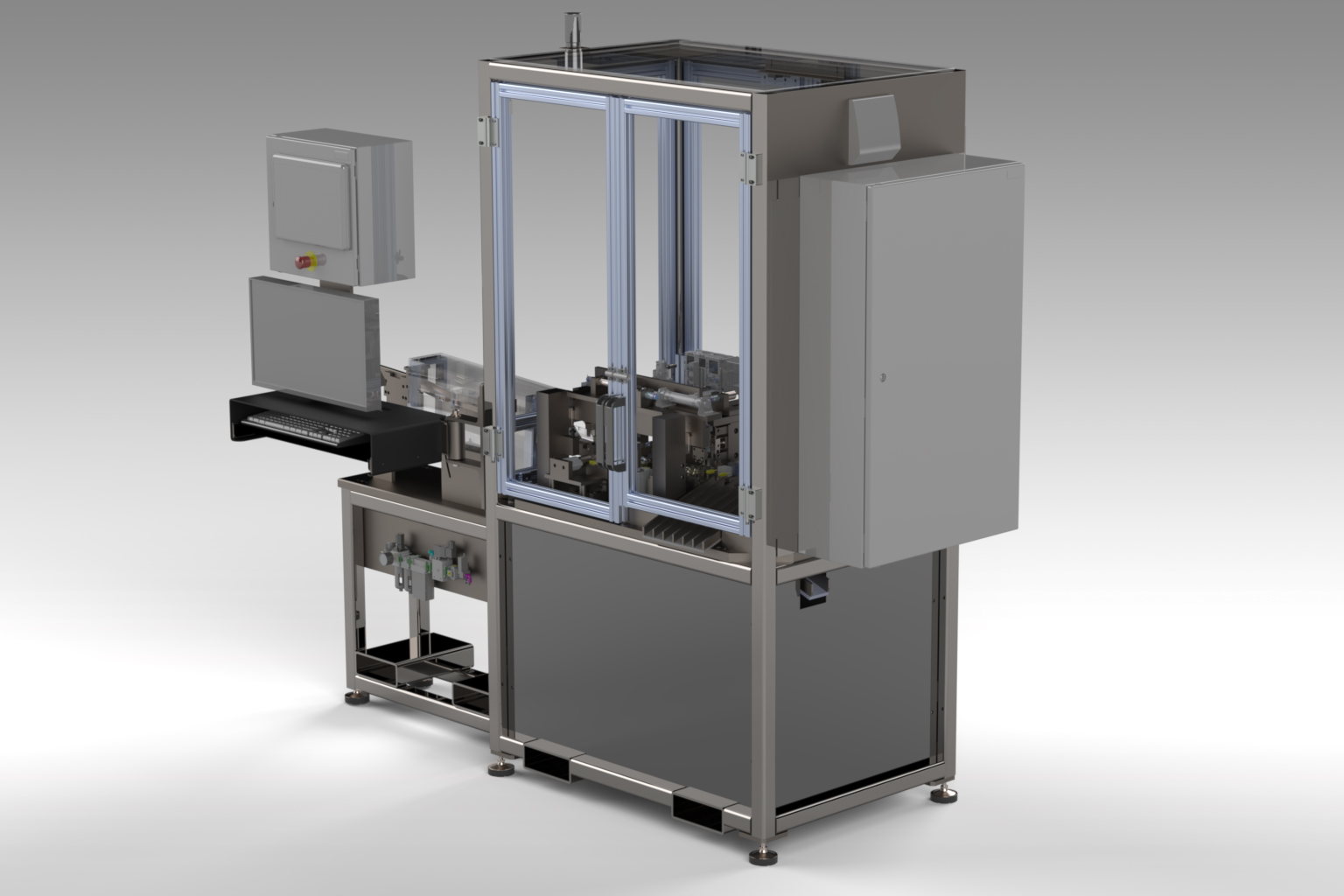
The Kurt Gaging Process
Consultative Approach
Our process starts with understanding your timeline and project objectives.
Development Process
After consultation, all project parameters are brought to our design engineers. The design concept and proposal are created highlighting Kurt Gaging’s solution and ROI for the client.
Runoff
When the project is complete a runoff will be completed either at Kurt Gaging or on the client’s facility. Often both locations are required to meet a project’s GR&R requirements. Repeatability and correlation data gathered and presented to the client for approval.
Start Up, Installation and Training
Kurt Gaging engineer will be on-site to start up, commission gage, train the client’s staff in operation and maintenance of gaging system.
Service and Support After the Sale
We provide excellent “service after the sale.” Phone support, documentation, annual calibrations and regular SPC-training classes all combine to build long-term partnerships with clients and to keep their gaging system operating accurately for years.